We are pleased to announce that we will be exhibiting at Global Industrie! 📅 When? March 11-14, 2025 at Lyon Eurexpo📍 Where to find us? Stand 1J16 Why visit our stand? Discover our innovative solutions forautomation, MoM/MES and digitalization/IA Attend live...
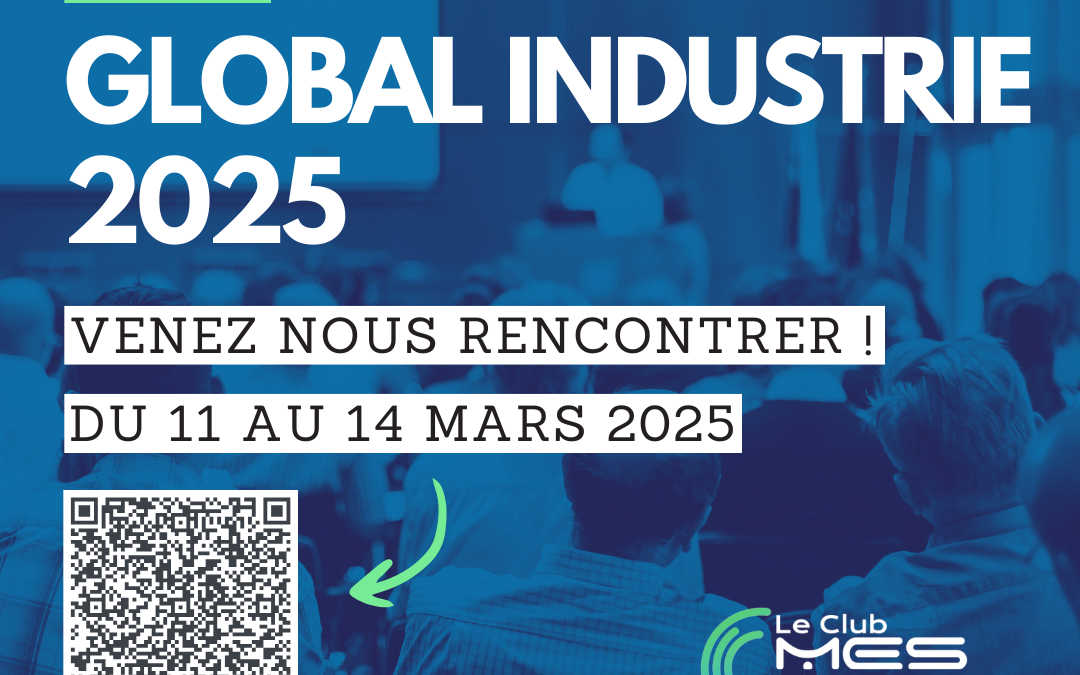